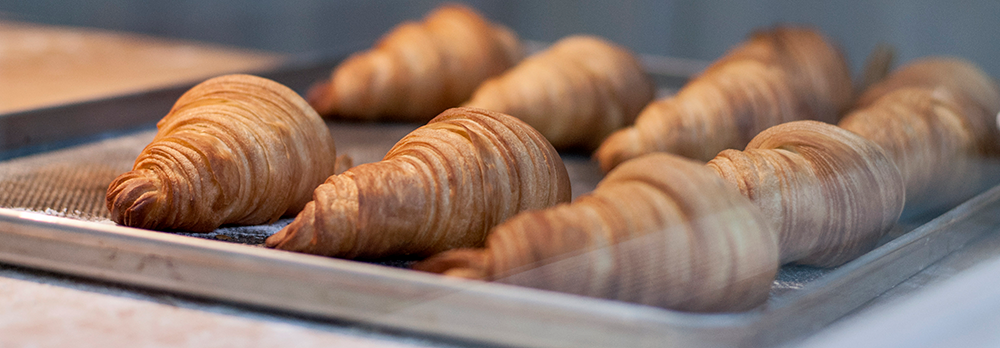
The problem
Croissant manufactured with the moulded ends joining to form a circle tended to open out during baking but the effect is not consistent from piece to piece.
The Cause
Uneven tensions set up in the paste sheet during processing.
The explanation
During processing, the rheology of the laminated paste changes during sheeting. In particular there is a tendency for the gluten network in the base dough to be aligned in the direction of sheeting. The stresses in the paste coming from this uni-directional sheeting are largely evened out by a combination of turning the paste through 90° and with rest periods between the various sheeting and laminating steps.
However, after the final paste reduction step, before cutting rolling and shaping, there is less opportunity to even out the uni-directional stress. The effect of this stress is often seen as the shrinkage of the pieces after they are cut from the paste sheet. In more shapes, such as croissant, other changes may be observed when the dough is too elastic and these may include the opening-out of the circular shape.
The solution
The degree of shape distortion will be significantly affected by the length of resting time after the paste leaves the final sheeting rolls; the longer the resting period, the less likely there will be shape distortion.
In some production units there is not the opportunity to have a long final resting stage and in these cases it can help to have a cross-roller. This is a small single roller which runs at right angles to the line of travel of the dough sheet. It is not intended to make a significant contribution to reducing the thickness of the sheet but it can help even out the stresses built-in during the final thickness reduction step and reduce the elastic nature of the paste sheet.
The variation in degree of croissant shape distortion is associated with the position of the cut triangle with the paste sheet. Some forms of overlapping during the laminating step leave behind a characteristic ‘WWWW’ pattern in the sheet which is exaggerated during subsequent thickness reduction. Depending where the triangle is cut from, this pattern affects the degree of distortion. Many factors influence the precise shape of the ‘WWWW’ pattern, not least the synchronisation of speeds through the laminating plant.